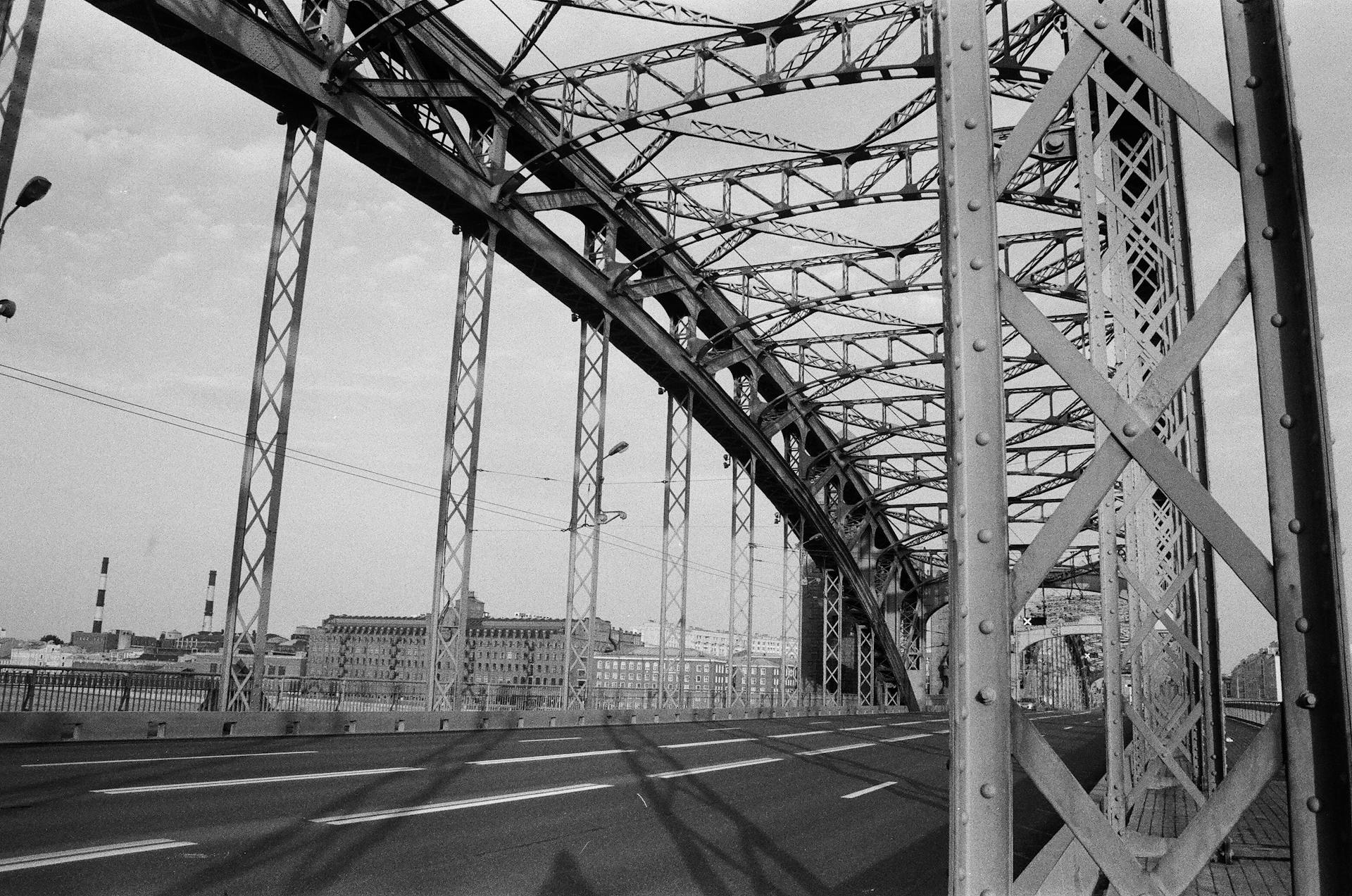
Designing a steel roof truss requires careful consideration of strength and efficiency. A steel roof truss can span up to 60 feet without intermediate supports.
The truss's strength is determined by its ability to resist various loads, including dead loads, live loads, and wind loads. The truss's efficiency is measured by its ability to minimize material usage while maintaining strength.
To achieve this balance, the truss's geometry must be carefully optimized, taking into account factors such as the spacing of the trusses, the depth of the truss, and the type of steel used.
Curious to learn more? Check out: Type B Roof Deck
Design Considerations
All purlins connected to a roof bracing can be considered as lateral rigid support points, while intermediate purlins can also be considered as a rigid point of support if the roof behaves as a diaphragm.
Lateral support points are provided to the lower chord by additional vertical bracing elements between trusses. This is crucial for ensuring the structural integrity of the truss.
For your interest: C Purlins Roof Design
A truss is typically designed to resist bending about the major axis only, but it's essential to consider any out-of-plane loading, which can cause bending about the minor axis. This includes loading normal to the plane of the truss and load reversals caused by wind uplift.
Here are some key factors to consider when specifying steel trusses:
- Any out-of-plane loading, i.e. loading normal to the plane of this truss, which causes bending about the minor axis, must be carefully considered.
- Load reversals e.g. caused by wind uplift could cause tension members to experience compression and vice versa.
- Application of load away from node points as this will induce local bending in individual truss elements.
Factors in Design
Design considerations for any project are crucial, and steel trusses are no exception. Structural designers must consider several essential factors to ensure the roof is safe and durable.
One key factor is the load and stresses the roof will be subjected to over time. This includes factors like wind, snow, and weight of the structure itself.
Structural strength is a top priority in truss design. Trusses are incredibly strong for their weight, allowing for long spans without interior supports.
The use of steel trusses can also be cost-effective. Since trusses use fewer materials while maintaining strength, they often reduce material costs.
Time efficiency is another benefit of truss design. Prefabricating trusses off-site reduces labor costs and accelerates project completion.
In creative applications, trusses can be left exposed to create a warm and inviting interior aesthetic.
Take a look at this: Types of Timber Roof Trusses
Material Selection
Choosing the right material for your steel roof truss is crucial, as it determines the overall strength and durability of the roof. The American standard AISC 360-22: Specification for Structural Steel Buildings provides guidelines for the steel's minimum yield strength and other properties.
A36 is the most commonly used structural steel grade, with a minimum yield strength of 250 MPa (36,300 psi). It's suitable for most truss applications, particularly where the load is not too high.
A572 is used for heavy loads requiring higher strength and is available in several grades, including 42, 50, 55, 60, and 65. This grade offers increased strength over A36.
A992 has a minimum yield strength of 345 MPa (50,000 psi) and a higher strength-to-weight ratio than A36 and A572, making it suitable for long-span trusses with heavy loads.
A500 is a carbon steel grade generally used in steel tubing, where truss elements are typically made. This grade has multiple grades and classes depending on the section constructed.
Here are some key properties of the mentioned steel grades:
- A36: 250 MPa (36,300 psi) minimum yield strength, suitable for most truss applications.
- A572: Available in several grades, including 42, 50, 55, 60, and 65, used for heavy loads requiring higher strength.
- A992: 345 MPa (50,000 psi) minimum yield strength, suitable for long-span trusses with heavy loads.
- A500: Multiple grades and classes, used in steel tubing for truss elements.
The selection of the material is typically based on the availability in the market and the intended level of stress to be applied.
Design Considerations
When designing a truss, it's essential to consider the type of truss configuration that suits your project's needs.
Trusses can vary greatly in geometry and element choice, so it's crucial to choose the right type for your project. Different truss configurations serve specific purposes, depending on the structural requirements, aesthetic goals, and functional needs of a project.
For short-span high-pitched roofs, a Fink truss is a great option, as it offers economy in terms of steel weight by subdividing members into shorter elements.
The choice of truss type ultimately depends on the project's requirements, but understanding the different types and their applications can make all the difference in achieving a successful design.
Here's an interesting read: Type a Roof Deck
Saw-Tooth
The saw-tooth truss is a variation of the North light truss commonly used in multi-bay buildings.
It's similar to the North light truss in that it often includes a truss of the vertical face running perpendicular to the plane of the saw-tooth truss.
This design allows for a unique and functional layout that can be adapted to various building needs.
A key characteristic of the saw-tooth truss is its ability to support multi-bay buildings.
It's a versatile option for architects and builders looking to create a specific aesthetic or functional space.
Elements Considerations
Elements Considerations are crucial in designing a steel roof truss. The type of support provided to the truss members is a key consideration.
All purlins connected to a roof bracing can be considered as lateral rigid support points. This is a common design approach.
Intermediate purlins can also be considered as a rigid point of support if the roof behaves as a diaphragm. This is in accordance with BS EN 1993-1-3.
Lateral support points are provided to the lower chord by additional vertical bracing elements between trusses. This adds stability to the structure.
Here are some key considerations for elements in a steel roof truss:
- Purlins connected to roof bracing: lateral rigid support points
- Intermediate purlins: rigid point of support (if roof behaves as a diaphragm)
- Lower chord: lateral support points provided by vertical bracing elements
Modular Systems
Modular Systems are a game-changer in construction, allowing for flexibility and speed in building projects. Prefabricated modular trusses are a great example, reducing on-site construction time and labor costs.
These trusses are pre-engineered and assembled in factories, which improves precision and consistency. This level of quality control is hard to match on-site, where human error can creep in.
Modular trusses are also more efficient in terms of material usage, which can lead to cost savings for builders. By reducing waste and optimizing material usage, builders can pass the savings on to their clients.
As an added bonus, modular trusses can be designed to meet specific building codes and regulations, ensuring compliance without the need for costly rework.
Take a look at this: Trusses and Purlins
Design Process
The design process for a steel roof truss involves several key steps. We start by modeling the truss as a simply supported beam member to calculate the global bending moment and shear force.
To determine the depth of the truss, we need to assess any restrictions on the depth and calculate the chord force, Nchord. This value is used to select a suitable chord member, Ach,i, which should be checked against Eurocode 3 compression member checks.
The chord member size and truss depth are then used to calculate the value of III, which is used to determine the maximum deflection of the truss member. If the deflection is within acceptable limits, the chosen values are accepted; otherwise, we need to adjust the truss depth and/or chord member size.
Here are the steps to calculate the deflection of the truss member:
- Calculate the value of III using the chosen Ach,i and HHH values.
- Use the reduced elastic modulus, E∗=160000N/mm2, to determine the maximum deflection.
- Compare the calculated deflection to acceptable limits, such as L/250 or L/500.
Geometry
Geometry plays a crucial role in the design process of a steel roof truss. The physical dimensions and layout of a truss structure, known as truss geometry, are determined by the specifications of the structure it is intended to support.
The height of a roof truss is typically based on the desired slope or pitch of the roof. The width of a truss can vary depending on the design and load-bearing requirements of the structure.
In general, a truss is composed of a series of interconnected triangles that distribute weight and stress evenly throughout the structure. The number of triangles, and therefore the number of unit panels, depends on the size and shape of the truss.
Here are some key parameters that influence truss geometry:
- Span of roof truss
- Spacing of the trusses
- Nodal spacing along the trusses
- Spacing of out-of-plane bracing of chords
These parameters can vary depending on the architectural context, owner's preferences, and structural and construction limitations. The truss geometry selected must be followed closely to ensure that the truss is designed to provide adequate strength and stability while minimizing the amount of material required.
Calculating Total Distributed
Calculating Total Distributed Loads is a crucial step in the design process. The gravity loads, including dead and live loads, are typically applied to the top and bottom chords of a truss.
In a pitched roof truss, the gravity loads are applied to the top chord of the truss. The bottom chord may also be designed to resist the weight of any occupants or equipment in the attic space.
For floor trusses, the gravity loads are typically applied to the top chord, while the bottom chord carries the weight of occupants, furniture, and other moveable objects. The dead load is usually 342 lb/ft, while the live load is 154 lb/ft.
Explore further: Load Bearing Roof Truss
The load combination is calculated using the equation 1.2 Dead load + 1.6 Live load, as recommended by the American standard. This is used to determine the total distributed load on the truss.
The maximum axial load on the truss is approximately 14,400 kN and 12,700 kN for compression and tension.
Intriguing read: Calculating Snow Load on Pitched Roof
Pratt ('N')
Pratt trusses are a type of truss commonly used in long span buildings ranging from 20 to 100 m in span.
In a conventional Pratt truss, diagonal members are in tension for gravity loads. This type of truss is used where gravity loads are predominant.
You can also use an alternative Pratt truss where the diagonal members are in tension for uplift loads, which may be the case in open buildings such as aircraft hangers.
To add extra support to a Pratt truss, you can add secondary members to create intermediate support points for applied loads.
Secondary members can also help limit the buckling length of members in compression, which is especially useful in 2D trusses where buckling is only modified in one axis.
A Pratt truss can have either a single or a double slope to the upper chord of a roof supporting truss.
Here are some common types of Pratt trusses:
- Pratt truss (gravity l
Pratt truss (uplift loads)
Pratt truss with secondary members
Duo-pitch Pratt truss
Modelling
Modelling is a crucial step in the design process, and it's essential to get it right to ensure your truss structure is safe and efficient. Typically, it's convenient to work with restricted models, such as 2D models, rather than a global 3D model.
For a standard building, a 2D model of the portal, wind girder, and vertical bracing is usually sufficient and justified. A truss can be modelled without its supporting columns when it is articulated to the columns.
When separate models are used, it may be necessary to combine the results of several analyses to verify the resistance of certain elements. For example, the upper chord of a truss that also serves as the chord of the wind girder.
A global 3D model can be used, but if member releases are not provided, 'parasitic' bending can be observed, which often only creates an illusion of precision in the structural behavior.
For another approach, see: Architectural Design 3d Models
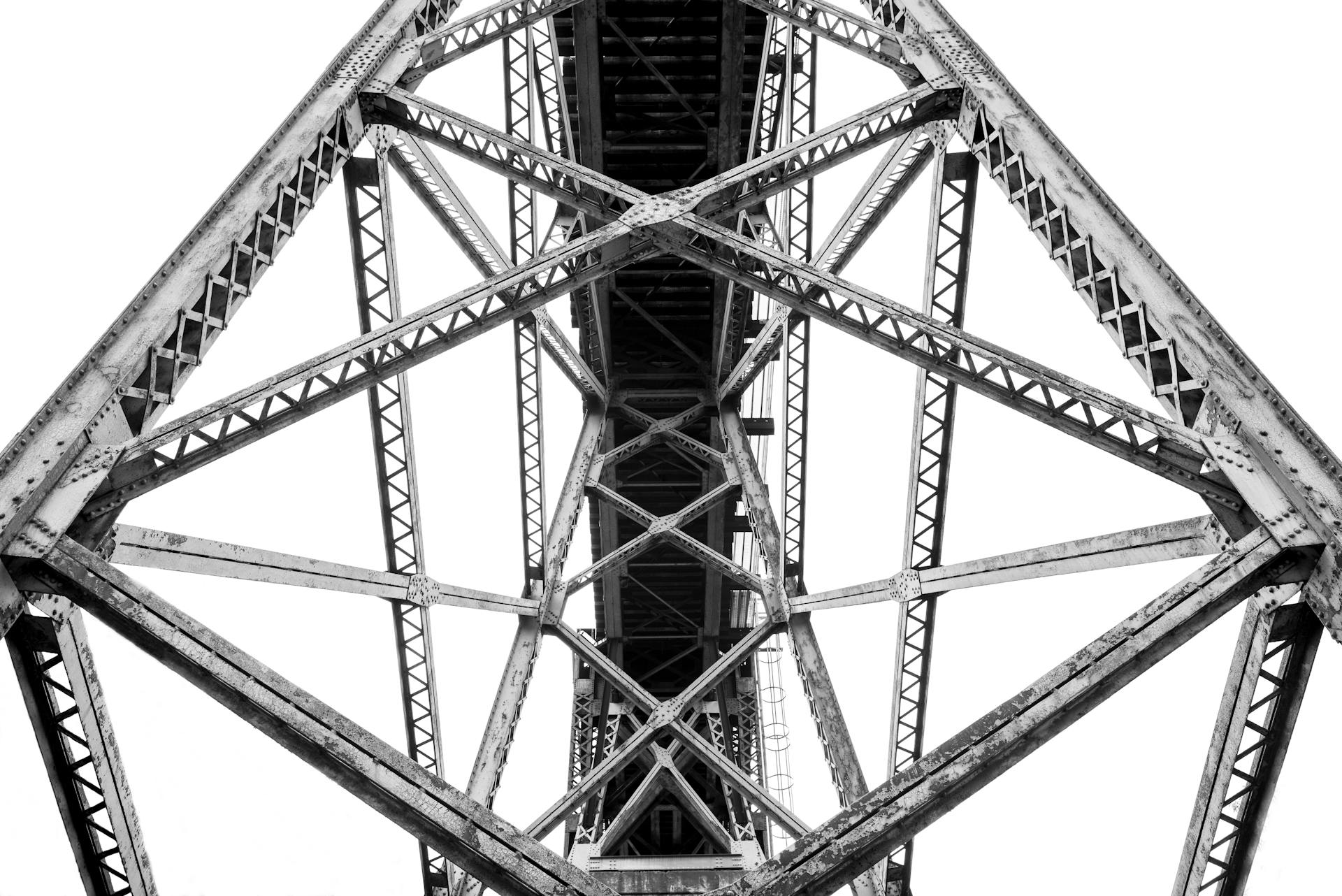
Two analysis models are commonly used for trusses: continuous chords with pinned internals, or pinned joints throughout the truss.
Here are the two analysis models commonly used for trusses:
Use of Vierendeel
Vierendeel trusses are rigidly-jointed trusses with only vertical members between the top and bottom chords, which are normally parallel or near parallel.
Their design differs from conventional trusses, where members are primarily designed for axial loads, but in Vierendeel trusses, elements are subjected to bending, axial force, and shear.
Vierendeel trusses are usually more expensive than conventional trusses, which is a significant consideration for any design project.
Vertical members near the supports are subject to the highest moments, requiring larger sections to be used than those at mid-span.
Considerable bending moments must be transferred between the verticals and the chords, which can result in expensive stiffened details.
Their moment-resisting capability makes them a unique option for certain design situations.
Consider reading: Exposed Timber Roof Trusses
Initial Sizing Workflow
The initial sizing workflow is a crucial step in the design process. It's where you determine the basic dimensions of your truss.
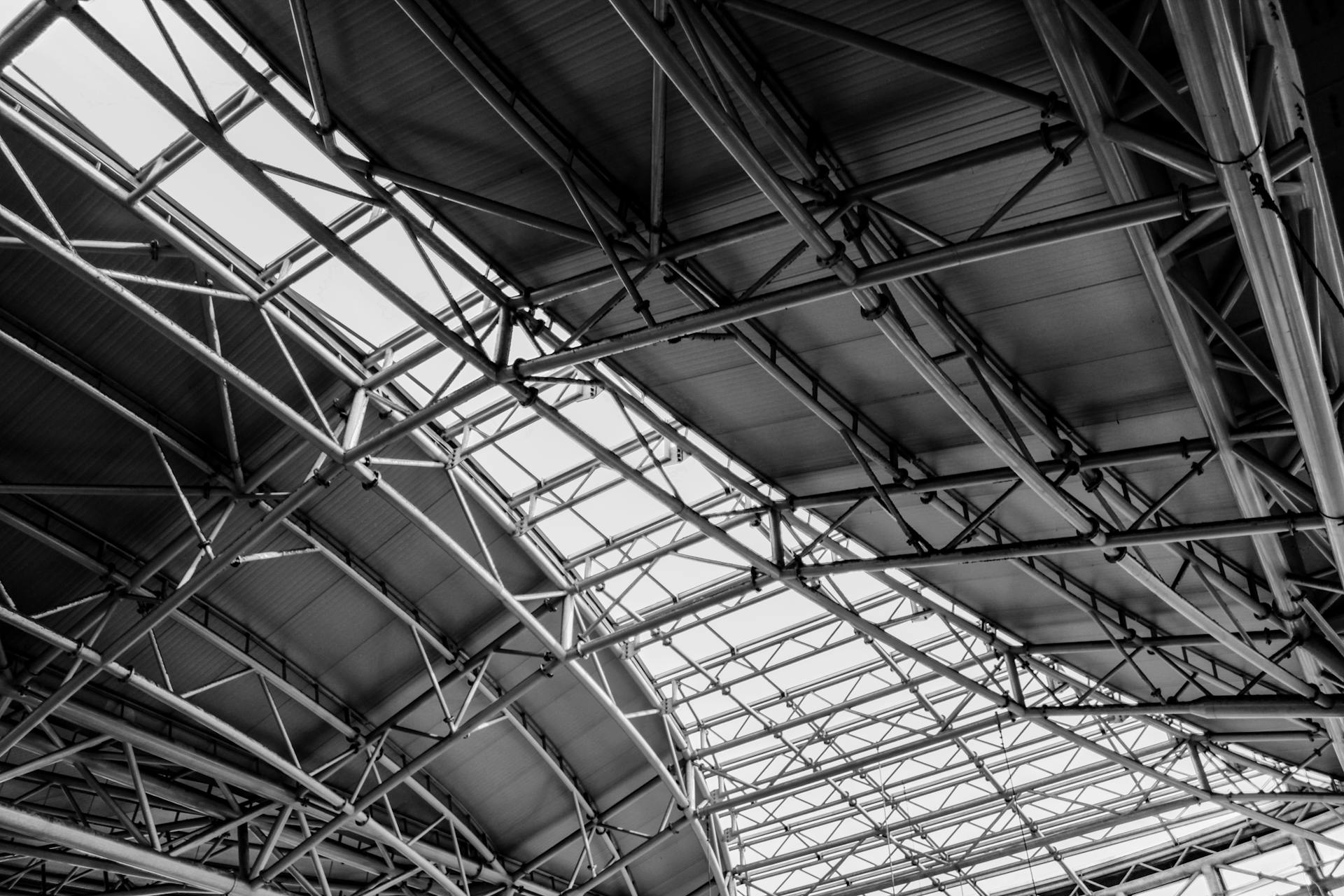
To start, you'll model your truss as a simply supported beam member and calculate the global bending moment and shear force. This will give you a solid foundation for the rest of the process.
The next step is to assess any restrictions on the depth of the truss. This is important because it will impact the overall size and stability of your truss.
Here's a breakdown of the steps involved in the initial sizing workflow:
The goal of this workflow is to find a balance between size and stability. By following these steps, you'll be able to determine the initial dimensions of your truss and set the stage for further design and analysis.
Automation in Fabrication
Automation in fabrication is revolutionizing the design process, allowing for greater precision and efficiency.
AI-powered robots are now automating the fabrication of trusses, making precise cuts and assembling components faster and with greater accuracy than human workers.
This automation reduces the risk of errors and speeds up production, making it a game-changer for truss fabrication.
AI-guided machinery can also adjust in real-time to optimize material usage, increasing efficiency in truss production.
Human-AI Collaboration
Human-AI Collaboration is a game-changer in the design process. It's a partnership between humans and AI systems that leads to faster and more innovative solutions.
AI tools can suggest optimal truss designs based on predefined parameters, freeing up engineers to focus on higher-level decisions. This collaboration can lead to more efficient design iterations.
One exciting example is the collaboration between human engineers and AI systems in truss design. Engineers can work with AI tools that suggest optimal truss designs based on predefined parameters.
By working together, humans and AI systems can create more innovative and effective designs. This interactive process allows for real-time adjustments and feedback, leading to stronger and more durable structures.
AI systems can adjust in real-time based on feedback, such as strengthening certain parts of the truss or adjusting load distribution. This leads to faster design iterations and more innovative solutions.
Worth a look: Shed Roof Design for Porch
Structural System
Trusses as a structural system have their strengths and weaknesses. They're a popular choice for building roofs due to their ability to span long distances with minimal support.
Trusses can be made up of various materials, but in the context of steel roof truss design, they're often made from steel. Prefabricated modular trusses are becoming more popular due to their flexibility and speed in construction.
In-plane buckling is a concern when designing trusses, and it's essential to consider this when determining the axial forces. With a critical length of 1.148m, you can ensure that your truss design is stable and secure.
Warren
Warren trusses are commonly used in long span buildings ranging from 20 to 100 m in span.
They have a unique design where diagonal members are alternatively in tension and in compression.
The Warren truss has equal length compression and tension web members, which is a key feature of this type of truss.
This design allows for a more efficient use of materials and can be more cost-effective than other types of trusses.
Warren trusses are also used for the horizontal truss of gantry/crane girders, showcasing their versatility in different applications.
A modified Warren truss may be adopted where additional members are introduced to provide a node at locations such as purlin locations.
Discover more: 2x4 Roof Truss Span Chart
North Light
North Light trusses are traditionally used for short spans in industrial workshop-type buildings.
They allow maximum benefit to be gained from natural lighting by using glazing on the steeper pitch which generally faces north or north-east to reduce solar gain.
North Light trusses typically have a truss running perpendicular to the plane of the North Light truss, to provide large column-free spaces.
This design can increase the volume of the building, which can also increase the demand for space heating.
Using north lights to increase natural daylighting can reduce the operational carbon emissions of buildings, but their impact should be explored using dynamic thermal modelling.
Take a look at this: Gambrel Roof Steel Buildings
Vierendeel
Vierendeel trusses are rigidly-jointed trusses with only vertical members between the top and bottom chords. The chords are normally parallel or near parallel.
These trusses are subjected to bending, axial force, and shear, unlike conventional trusses with diagonal web members.
Vierendeel trusses are more expensive than conventional trusses and are typically used in instances where diagonal web members are obtrusive or undesirable.
Vertical members near the supports in Vierendeel trusses are subject to the highest moments and require larger sections to be used than those at mid-span.
Connections
Connections are a crucial part of a structural system, and there are several types to consider. Bolted and welded connections can both be used, but bolted site splices are often preferred for their economy and speed of erection.
In steelwork construction, bolted connections are commonly used for open sections, which may involve the use of gusset plates. Guidance on the design of welded joints for certain hollow sections is available from Tata Steel.
Welded connections are often used in Vierendeel trusses due to their rigid joints, which must transfer significant bending moments. If joints are bolted, substantial connections will be necessary, generally using pre-loaded assemblies.
Pre-loaded assemblies are recommended to eliminate the consequences of slip and bearing deformation in connections. This is especially important in light roof trusses, where entirely bolted connections are less favored due to the requirement for gusset plates and their increased fabrication costs.
Here are some common types of connections:
- Bolted connections
- Welded connections
- Pre-loaded assemblies
- Welded sub-assemblies
It's essential to use proper truss connector plates or bolts that are suited to the materials being joined. Misalignment or weak connections between trusses and other structural components can lead to long-term failure, often due to poor workmanship or inadequate fasteners.
Tension Member
Our tension member calculations are simplified when chord members are connected by welding, which means no bolt holes in the section.
This assumption is crucial because it eliminates the need to account for bolt holes, making the calculation process more straightforward.
We're looking at the gross section capacity in this scenario, which is a key factor in determining the tension member's capacity.
The absence of bolt holes also means we don't have to consider the reduced cross-sectional area caused by holes, making the calculation even simpler.
In a welded connection, the chord members are directly connected, which eliminates the need for bolts and the associated calculations.
Readers also liked: Parallel Chord Truss Roof
Design and Analysis
Structural analysis for each load combination is a crucial step in steel roof truss design, yielding the member actions used in design.
For this purpose, we'll assume that you're comfortable determining the axial forces. If not, you can refer to the various tutorials referenced above.
Lcr, the critical length for in-plane buckling, is calculated as 0.9 times the length of the member, in this case, 1.275 meters.
Calculate Nrd
To calculate the cross-sectional resistance of the section, you need to follow the guidelines from Annex BB of BS EN 1993-1-1. The buckling length for buckling in the plane of the truss of the chord members can be taken as 90% of its system length.
The buckling length is a crucial factor in determining the resistance of the section. For out-of-plane buckling, the buckling length must be taken as the distance between lateral support points.
In this case, the buckling length for out-of-plane buckling is given as Lcr = 2.550m. This value is used to determine the cross-sectional resistance of the section.
Intriguing read: Gable End Overhang Length
Check Ned > Nb, Rd
To check if a proposed chord member is okay in compression, we need to make sure it can handle the expected forces. This involves comparing the effective axial force (NEd) to the buckling resistance (Nb,Rd).
The effective axial force is calculated by multiplying the load factor by the critical load. For example, if we're working with a load factor of 0.9 and a critical load of 1.275m, we get NEd = 1.148m.
The buckling resistance is the minimum value that the member can withstand without buckling. It's essential to ensure that NEd is greater than Nb,Rd for the member to be safe in compression.
Eurocode 3
Eurocode 3 is a crucial part of designing steel roof trusses. It's a set of standards that ensures the truss can withstand various loads and stresses.
To design a steel truss to Eurocode 3, we need to consider the compression and tension forces acting on the members. We'll assume that the joints between individual truss members act as ideal pins, simplifying the design process.
For chord members, we'll design them to resist both compression and tension forces. This ensures that both the top and bottom chords provide adequate resistance to the internal forces. Typically, all chord members will have the same section size in a truss which is subject to load reversals.
Here's a summary of the properties of the assumed S355 100x100x8 hot-finished square hollow section (SHS) for both the top and bottom chords:
- Depth, d = 100 mm
- Width, b = 100 mm
- Thickness, t = 8 mm
- Area, A = 28.8 cm²
- Second moment of area, I = 400 cm⁴
- Radius of gyration, r = 3.73 cm
- Elastic modulus, Z = 79.9 cm³
- Plastic modulus, S = 98.2 cm³
Fire Resistance
Fire Resistance is crucial in steel roof truss design, particularly in the US, where it must meet certain fire resistance ratings specified in American standards such as AISC 360 and NFPA's standards NFPA 5000 and NFPA 220.
These standards dictate the minimum requirements for fire resistance in building construction, and failure to comply can have severe consequences. Fire resistance ratings are essential for ensuring the safety of occupants and property in the event of a fire.
Structural Analysis
Structural analysis is a crucial step in steel roof truss design. We'll assume you're comfortable determining axial forces, so let's dive into the next step.
To perform structural analysis, we'll use a matrix-based approach for larger or statically indeterminate trusses. This is because manual methods can be time-consuming and prone to errors.
For in-plane buckling, we'll calculate the critical length, Lcr, which is 1.148 meters in this example. This value is essential for determining the member actions that will be used in design.
Non-Assembly Deflection
The clearance introduced into bolted connections can have a significant effect on displacement of the nodes.
For standard bolt sizes, holes which are 2 mm larger than the bolt are usually made, introducing clearance that allows slip.
Slip can be considered as an additional extension that is added to the elastic elongation of the member in tension, or a reduction in length that is added to the elastic shortening of the compressed member.
The total slip in the many different connections of a truss structure can lead to a significant increase in displacements.
In most cases, the visual effect is the worst consequence, but increased deflection can lead to a reduction of free height under the bottom chord.
This might prevent or upset the anticipated usage, such as the smooth operation of doors in an aeroplane hangar.
An increase in deflection can result in a reduction in the slope of the supported roof and even a slope inversion, increasing the risk of water ingress.
To control the effect of connection slip on displacements, it is often necessary to use preloaded bolts or welded connections instead of bolted connections.
Take a look at this: Lean to Shed Roof Slope
Accounting for Shear
In structural analysis, shear deformation is a crucial aspect to consider, especially in trusses where it's appreciable and can't be ignored.
The industry recognizes a simple approach to accounting for shear deformation in trusses, which involves reducing the modulus of elasticity (EEE) from 210000N/mm2 to 160000N/mm2.
For standard truss configurations with adequately sized chords, this simplification is advisable.
Ignoring global shear deformation is acceptable in typical I-beam calculations, thanks to the Euler-Bernoulli beam theory assumption that plane sections remain plane.
In most cases, flexural deformation is significantly larger than shear deformation, making it acceptable to ignore shear deformation.
Deep beams used over short spans are an exception where shear deformation is not negligible.
Industrial Warehouse
Industrial Warehouse projects require careful consideration of load-bearing requirements, climate, and budget. The Texas-based project I mentioned earlier is a great example of this, where flat steel trusses were chosen for their ability to handle high loads while keeping the structure lightweight.
In areas with severe weather, like Texas, durability is essential. The steel trusses used in this project provided excellent durability, making it ideal for the site conditions.
To maximize usable space for storing heavy machinery and equipment, the builders opted for a flat steel truss design. This allowed for a large, open interior with minimal supporting columns.
The prefabricated trusses used in this project sped up installation, reducing labor costs and the overall timeline.
Load Considerations
A truss is typically designed to resist bending about its major axis only, so any out-of-plane loading must be carefully considered. This means thinking about loads that are applied normal to the plane of the truss.
Load reversals, such as those caused by wind uplift, can cause tension members to experience compression and vice versa. This is not necessarily a big problem, but it's a factor that needs to be considered.
Application of load away from node points can induce local bending in individual truss elements, which can affect the overall structure. This is something to keep in mind when designing a steel roof truss.
Here are some key factors to consider when specifying steel trusses:
- Out-of-plane loading
- Load reversals
- Application of load away from node points
- Structural applications involving very large shear forces
Permanent Actions
Permanent actions are a crucial part of load considerations. They include the self-weight of various structural elements.
The self-weight of an aluminium roofing sheet is a key permanent action. It comes in at 0.022kN/m2.
You also have the weight of the ceiling below the roof truss, which is 0.068kN/m2. Then there's the weight of services, which is a significant 0.1kN/m2.
Purlins, spanning between trusses, add 0.162kN/m2 to the total permanent loads. The self-weight of trusses itself is 0.22kN/m2.
Here's a breakdown of the different permanent loads:
- Self-weight of aluminium roofing sheet: 0.022kN/m2
- Weight of ceiling (below the roof truss): 0.068kN/m2
- Weight of services: 0.1kN/m2
- Weight of purlins (spanning between trusses): 0.162kN/m2
- Self-weight of trusses: 0.22kN/m2
The total permanent loads come out to be 0.572kN/m2.
Combinations
Combinations are a crucial aspect of load considerations. In our previous example, we saw that we need to combine individual load cases into ultimate limit state loads.
We use factors such as γG=1.35 and γQ=1.50 to combine these loads. These factors are applied to the individual loads to determine the total load on the structure.
The combination of loads is not just a simple addition, but a careful consideration of various factors. In our example, we also saw the use of ψ0=0.9, which is a value from Table A1.1 of BS EN 1990: 2002.
The combination of loads is a critical step in ensuring the safety and integrity of a structure. By carefully combining individual loads, we can determine the total load that a structure can withstand.
In our example, we considered three individual load cases, which were combined using the given factors. This process helps us to accurately determine the ultimate limit state loads on a structure.
Permanent Wind Load
The Permanent Wind Load is a crucial consideration in load calculations. For Load Case 3, Permanent Load + Wind Load, we have a favourable factor of 1.00 for the permanent load and a factor of 1.50 for the wind load.
The wind load is calculated using wind pressure for components and cladding, as per Chapter 30 of ASCE 7-16. We'll be using the SkyCiv Load Generator to calculate the wind loads acting on the roof trusses.
The location of the structure is at 8050 SW Beaverton Hillsdale Hwy, Portland, OR 97225, USA, with a risk category of I (Garage). The building dimensions are 10.0 m in length, 7.0 m in width, and 5.0 m in mean roof height, with a roof angle of 29.745°.
For the wind load calculation, we set the Type of Structure to ASCE 7-16 – Buildings – Components and Cladding and the Enclosure Classification to Open Buildings. We also set the Wind Blockage to “Clear or Empty Under” as the cars below would not block more than 50% of the wind area below.
Recommended read: Components of a Roof Truss
The effective wind area for the roof truss is calculated as the spacing times the length, which is 23.31 m². However, according to Section 26.2 of ASCE 7-16, the effective width need not be less than one-third of the span length, which is also 23.31 m².
The design wind pressures can be calculated from the wind parameters, which are:
Since the wind pressures for zones 1, 2, and 3 are all the same, we can simplify our calculations. We'll have two cases: the positive (or max) case and negative (or min) case.
The positive wind load is 2.168 kN/m, acting towards and perpendicular to the roof surface, while the negative wind load is -1.508 kN/m, acting away and perpendicular to the roof surface.
For another approach, see: 2 Car Gambrel Garage
Sources
- https://clearcalcs.com/blog/practical-analysis-and-design-of-steel-roof-truss-according-to-american-standards
- https://steelconstruction.info/Trusses
- https://www.engineeringskills.com/posts/steel-truss-design
- https://skyciv.com/docs/tutorials/truss-tutorials/roof-truss-design-example/
- https://www.architecturecourses.org/build/truss-design-101
Featured Images: pexels.com