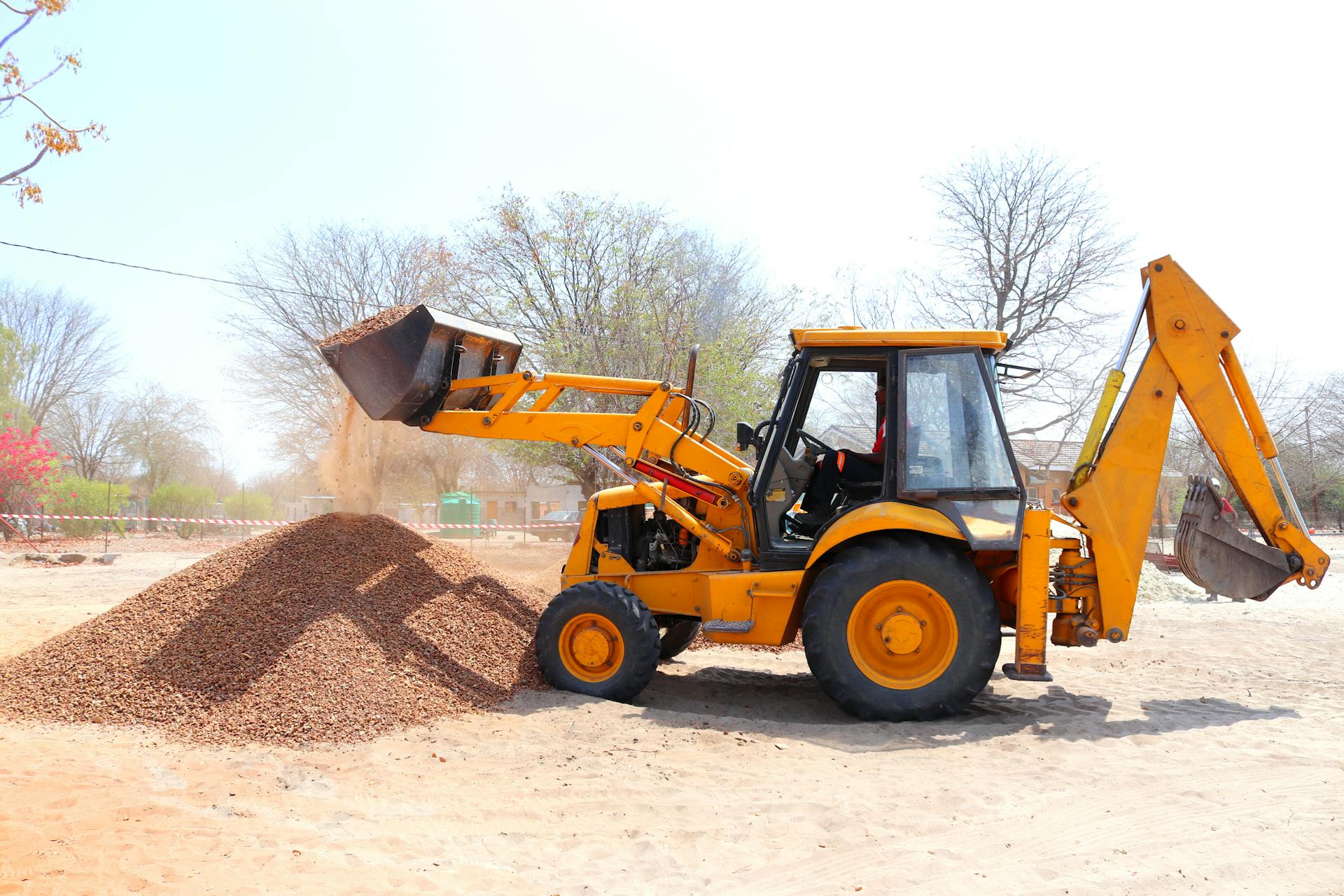
Load bearing roof trusses are the backbone of many homes, providing structural support and stability.
A well-designed load bearing roof truss can withstand a maximum load of 4,000 pounds per linear foot.
For a typical two-story home, the load bearing roof truss spans around 20 to 30 feet.
The design and construction of load bearing roof trusses involve a combination of wood and metal components.
Broaden your view: Hip Roof Load Bearing
Designing a Roof
Designing a roof truss requires careful consideration of various factors, including the location, building size, and roof angle. In this case, we're designing a roof truss for a garage in Portland, Oregon, with a building length of 10.0m and a building width of 7.0m.
To determine the roof loads, we need to assess the wind load and snow load acting on the roof trusses. The wind load to be used here will be for Components and Cladding, and we'll use ASCE 7-16 LRFD Load Combinations. We'll assume the following loads to be carried by the roof trusses: wind load and snow load.
Expand your knowledge: Calculating Snow Load on Pitched Roof
The roof truss will be designed using the SkyCiv S3D software, and we'll analyze it as a simply-supported truss assembly. We'll use an L shape (AISC) section for the roof truss, isolating the critical truss (spaced at 3.33m) and analyzing it as a simply-supported truss assembly.
Here are the key components of a roof truss:
- Apex: the top-most point of a roof truss
- Bottom Chord: the long horizontal beam that defines the lower edge of a truss
- Girder: a main roof truss that supports any secondary trusses framing into it
- Heel: a joint in a pitched roof truss where the top and bottom chords meet
- Overhang: the extension of the top chord beyond the heel joint
- Purlin: a smaller beam that runs perpendicular to the top chords of each roof truss
- Top Chord: the top-most beam of a roof truss
- Web: beams that join top and bottom chords in a triangular pattern.
The roof truss will be designed to withstand the calculated loads, and we'll use the SkyCiv Member Design Module to select the appropriate section for the roof truss members. We'll use the AISC 360-16 LRFD standard for the design.
Roof Truss Basics
A roof truss is a prefabricated structural framework designed to support a roof, typically replacing traditional roof rafters. It's manufactured in a factory-controlled setting, reducing construction time, energy, and costs.
Roof trusses are made up of various components, including the apex, which is the top-most point of the truss, and the heel, where the top and bottom chords meet. The heel is a critical joint in a pitched roof truss.
For another approach, see: Roof Truss to Top Plate Connection
The top chord is the top-most beam of a roof truss, and in most common types, it's slanted and hangs over the side of the building. The bottom chord is the long horizontal beam that defines the lower edge of a truss and provides strong support.
Here are some key components of a roof truss:
- Apex: The top-most point of a roof truss
- Heel: The joint where the top and bottom chords meet
- Top Chord: The top-most beam of a roof truss
- Bottom Chord: The long horizontal beam that defines the lower edge of a truss
- Web: Beams that join top and bottom chords in a triangular pattern
What Is a Truss?
A truss is a structural component made up of straight, interlocking members that form a series of triangles. This is the basic definition of a truss, and it's what you'll find in buildings, bridges, and even the Eiffel Tower.
To be considered a truss, a structure must have only pinned connections, meaning the members are free to rotate at the joints. This is a crucial aspect of truss design.
Loads must be applied only at the joints and never in the middle of a straight member. This is why trusses are normally found near the top of a building, supporting either the second story or the roof.
Every straight member of a truss is either in tension or compression, which keeps the truss stable and enables it to support more weight than any single member could on its own.
Here are the two assumptions that need to be made to consider a structure a truss:
- The structure must have only pinned connections, meaning the members are free to rotate at the joints.
- Loads must be applied only at the joints and never in the middle of a straight member.
These assumptions are key to understanding how trusses work and why they're such an effective way to distribute loads.
Factors Affecting Capacity
Material greatly affects a truss's load capacity, with different materials like steel, wood, and engineered wood products having varying capacities.
The design of a truss also plays a significant role, with various designs such as Howe trusses, Fink trusses, and King Post Trusses each having their own strengths and weaknesses.
Spacing is crucial, as the closer trusses are set, the more evenly the load is distributed, resulting in higher capacity.
Load distribution is also important, as evenly distributing the load across the entire truss increases its load-bearing capacity.
Take a look at this: Types of Timber Roof Trusses
Span refers to the distance a truss can cover unsupported, and generally, a truss's load-bearing capacity decreases as the span increases.
Here's a summary of the factors affecting load capacity:
Modifying a truss in any way, such as cutting, drilling, or notching, can drastically reduce its load-bearing capacity, so it's essential to leave trusses as they are.
Roof Load Calculations
Calculating the load a roof truss can bear is crucial for ensuring the structure's stability and safety. To determine the load, you need to consider the dead load, live load, and environmental load.
The dead load consists of the weight of roofing materials, ceiling materials, insulation, and the truss system itself. This can be broken down into the weight of roof sheets and accessories (0.15 kPa applied at the top chord) and the weight of the ceiling (0.25 kPa applied at the bottom chord).
The live load, on the other hand, is the weight of people or other moving things that may occasionally go up on a roof, which is typically 0.96 kPa.
To calculate the total load, you need to consider the spacing between the trusses, which is typically 3.33m from center to center. For roof trusses, the superimposed dead load is calculated as follows:
Live
Live loads are a crucial consideration in roof load calculations. The live load for roofs is equal to 0.96 kPa, according to ASCE 7-16. This value is applied to the horizontal projection of the area.
For roof trusses, the live load is calculated by multiplying the load by the spacing between trusses. In this case, the spacing is 3.33m from center to center, which is the critical member. This results in a live load of 3.197 kN/m.
To determine the live load acting on the roof truss, we need to consider the horizontal projection of the area. This load is then applied to the top chord nodes.
Here's a breakdown of the live load calculation:
Wind
Wind loads play a crucial role in roof load calculations, especially for open-pitched or duopicth roofs like the one in our garage example. The wind load to be used here will be for Components and Cladding for designing the roof truss members.
To calculate the wind load, we need to consider the wind pressure calculation for components and cladding, as specified in Chapter 30 of ASCE 7-16. The location of the structure, which is 8050 SW Beaverton Hillsdale Hwy, Portland, OR 97225, USA, is an important factor in determining the wind load.
The building length, building width, mean roof height, and roof angle are also critical parameters in the wind load calculation. For our garage example, the building length is 10.0 m, building width is 7.0 m, mean roof height is 5.0 m, and roof angle is 29.745°.
The wind blockage is an essential factor to consider, especially during typhoons when cars below may not block more than 50% of the wind area. In our example, we set the Wind Blockage to "Clear or Empty Under" to account for this.
The effective wind area for the roof truss can be calculated by multiplying the spacing by the length. In our example, the effective wind area is 23.31 m², which is calculated as 3.33m x 7.0m.
Here is a summary of the wind parameters used in our calculation:
The design wind pressures can be calculated using the wind parameters, and we get two cases: the positive (or max) case and negative (or min) case. The positive case has a wind load of 2.168 kN/m, while the negative case has a wind load of -1.508 kN/m.
Snow
The snow load on your roof is a crucial factor to consider when designing your structure.
For a garage in an open space, the balanced snow load is equal to 0.23 kPa. This is the load on the purlins and roof trusses when the roof is not exposed to wind.
The snow load is acting on the horizontal projection of the effective area, but it should be converted into an inclined load acting on the top chord of the roof truss. This is done by dividing the load by the cosine of the roof's angle.
In an unbalanced case, the snow load on the purlins and roof trusses can vary significantly, with one side experiencing a load of 1.399 kN/m and the other side experiencing no load at all.
The angle of the roof affects the load on the trusses, with a 29.745° angle being used in the example. This angle is crucial in determining the load on the trusses and the purlins.
The section used in the unbalanced case - L2.5”x2.5”x3/16” - is adequate and passed the design checks.
If this caught your attention, see: Exposed Timber Roof Trusses
Roof Design Considerations
Roof trusses are designed to carry various loads, including roof loads. We'll assume the wind load to be used for designing roof truss members is for Components and Cladding.
The roof profile of the garage is an Open-Pitched/Duopicth, with the Building Length, L, being the distance perpendicular to the pitch of the roof, and the Mean Roof Height, h, is the average of eave height and roof apex height.
Roof trusses are analyzed in 2D by adding supports on each node with code RRFRRR to only fix the Z-axis displacement. The initial section used is an AISC L shape – 2.5”x2.5”x3/16”.
To design the roof truss member, we'll use the SkyCiv Member Design Module and select AISC 360-16 LRFD. We'll also apply the roof loads and multiply each load to the member length to convert it to nodal loads.
The apex of a roof truss is the top-most point, which can be the peak of a triangular roof truss or the top-center point of a truss with a flat roof. The bottom chord is the long horizontal beam that defines the lower edge of a truss.
Here's an interesting read: 16 Gambrel Truss Plans
A girder is a main roof truss that supports any secondary trusses framing into it. The overhang is the extension of the top chord beyond the heel joint, and it's how far the top chord hangs over its bearing support.
To ensure the roof truss is strong and stable, we need to consider the web, which includes beams that join top and bottom chords in a triangular pattern. These beams are capable of carrying tension and compression stress, which helps keep the truss from bending.
The top chord is the top-most beam of a roof truss, which is often slanted and hangs over the side of the building. A purlin is a smaller beam that runs perpendicular to the top chords of each roof truss, used to support the roof's decking.
Take a look at this: Parallel Chord Roof Truss
Frequently Asked Questions
How much weight can roof trusses hold?
Roof trusses can typically hold a dead load of 5-10 pounds per square foot, depending on the weight of materials attached to them
What is the dead load for roof trusses?
For roof trusses, the customary dead load is typically 20 pounds per square foot. This is a standard assumption in building design and construction.
Featured Images: pexels.com