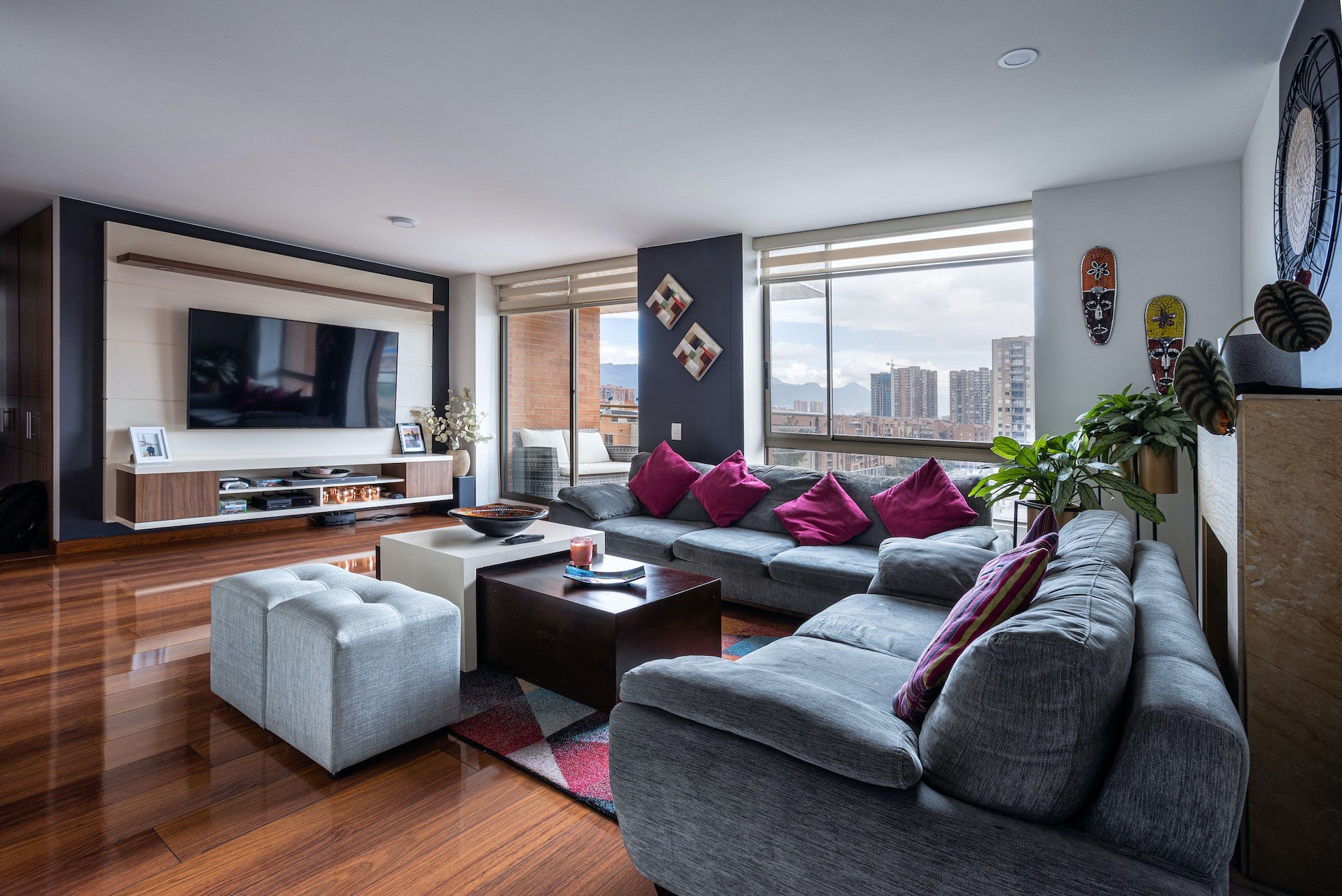
If you're looking to install a fuel pump in your truck bed, there are a few things to consider before you start cutting holes. First, you'll need to determine where the fuel pump will be located. It's important to choose a spot that is easily accessible and away from any potential hazards. Once you've selected the location, mark the spot with a pencil or marker.
Next, you'll need to choose the right size drill bit for the job. The size will depend on the size of the fuel pump you're installing. Once you've selected the correct size drill bit, attach it to your drill and begin drilling through the truck bed.
As you're drilling, be sure to go slowly and be careful not to damage the surrounding area. Once you've made it through the truck bed, insert the fuel pump into the hole. If everything fits correctly, you're ready to start installing the wiring.
If you're not comfortable doing the wiring yourself, you can always hire a professional to do it for you. However, if you're up for the challenge, it's not too difficult to wire the fuel pump yourself. Just be sure to follow the instructions that come with the fuel pump kit.
Once the wiring is complete, you can test the fuel pump to make sure it's working properly. To do this, simply turn on the ignition and wait for the pump to prime. If everything is working correctly, you should hear the pump running.
Now that you know how to install a fuel pump in your truck bed, you can get started on your project. Just be sure to take your time and be careful not to damage the truck bed. With a little bit of effort, you should be able to install the fuel pump without any problems.
Curious to learn more? Check out: Install Pendaliner Truck Bed Liner
Where is the best place to cut a hole in the truck bed for a fuel pump?
There is no definitive answer to this question as it depends on a number of factors, such as the make and model of the truck, the location of the fuel tank, and the preference of the individual cutting the hole. However, there are a few things to keep in mind that can help make the process easier and ensure a more professional-looking finished product.
When cutting a hole in the truck bed for a fuel pump, it is important to avoid the areas where the truck's frame is located. This will help prevent any potential damage to the frame, which could compromise the structural integrity of the truck. It is also important to avoid any electrical wiring or other components that could be damaged by the saw or drill used to cut the hole.
The size of the hole will also need to be considered. It should be large enough to accommodate the fuel pump, but not so large that it looks out of place or leaves the truck vulnerable to potential thieves. A hole that is too small can also make it difficult to properly install the fuel pump.
Once the decision on where to cut the hole has been made, the next step is to mark the area with a pencil or chalk. This will help ensure a straight, even cut when drilling or sawing. It is also important to take into account the location of the fuel tank when marking the hole, as the hole will need to be big enough to reach the tank.
Once the hole has been cut, it is important to smooth any rough edges with a file or sandpaper. This will help prevent the fuel pump from being damaged and will also make it easier to install.
Fuel pumps can be installed in a number of different ways, depending on the make and model of the truck. The most common method is to bolt the pump to the bed of the truck using the provided hardware. However, some models may require the use of special brackets or mounts. Consult the truck's owner's manual or a qualified mechanic for specific instructions on how to install the pump.
Curious to learn more? Check out: Metal Bed Frame
What are the dimensions of the hole that should be cut?
There are many factors to consider when deciding the dimensions of a hole to be cut. The size of the hole will depend on the purpose for which it is being cut, as well as the materials that will be used to fill the hole.
If the hole is being cut for a specific purpose, such as to install a door or window, the dimensions will be determined by the size of the opening. If the hole is being cut for a general purpose, such as to create a passage through a wall, the dimensions will be determined by the materials that will be used to fill the hole.
The thickness of the material that will be used to fill the hole will also affect the dimensions of the hole. If a thin material, such as drywall, is being used, the hole will need to be cut slightly larger than the material so that it can be fitted into the hole. If a thick material, such as concrete, is being used, the hole will need to be cut slightly smaller than the material so that it can be cast into the hole.
The type of tool that will be used to cut the hole will also affect the dimensions of the hole. A saw will create a hole that is slightly larger than the blade, while a router will create a hole that is slightly smaller than the bit.
In general, the dimensions of the hole should be cut so that the material can be fitted snugly into the hole. The hole should be cut to the appropriate size so that the material can be trimmed or sanded to create a perfect fit.
Discover more: Size Bed
How do you seal the hole around the fuel pump to prevent leaks?
The fuel pump is a critical component in any vehicle, and it is important to make sure that it is properly sealed to prevent leaks. There are a few different ways that you can seal the hole around the fuel pump to prevent leaks, and the best method will vary depending on the specific circumstances.
One method of sealing the hole around the fuel pump is to use a sealant. This can be a commercial sealant that you can purchase at a auto parts store, or it can be something as simple as a silicone sealant. Apply the sealant around the perimeter of the hole, and then allow it to dry. This will create a barrier that will prevent leaks.
Another method of sealing the hole around the fuel pump is to use a gasket. This is a piece of material, usually made of rubber or metal, that is placed between two surfaces to create a seal. You can purchase a gasket that is specifically designed for the fuel pump, or you can make your own out of a piece of flexible material.
If you are worried about leaks, you can also take some precautionary measures. For example, you can place a piece of tape over the hole. This will not completely prevent leaks, but it will help to reduce them. You can also try placing a rag over the hole. This will absorb any leaks that do occur.
No matter which method you choose, it is important to make sure that the hole around the fuel pump is properly sealed. Leaks can be dangerous, and they can also lead to expensive repairs. By taking the time to seal the hole, you can help to prevent these problems.
What type of fuel pump should be used for this installation?
There are many different types of fuel pumps, each designed for a specific installation. The most common type of fuel pump is the electric fuel pump. This type of fuel pump is typically used in vehicles with fuel injection systems. Electric fuel pumps are available in a variety of styles, including inline, canister, and barrel.
Inline fuel pumps are the most popular type of electric fuel pump. They are designed to be installed in the fuel line between the fuel tank and the engine. Inline fuel pumps are available in a variety of flow rates and pressures.
Canister fuel pumps are typically used in carbureted applications. They are designed to be mounted on the engine and connect to the carburetor with a fuel line. Canister fuel pumps are available in a variety of flow rates and pressures.
Barrel fuel pumps are typically used in high performance applications. They are designed to be mounted on the engine and connect to the fuel line with a fittings. Barrel fuel pumps are available in a variety of flow rates and pressures.
What is the maximum length of fuel hose that can be used with this installation?
The maximum length of fuel hose that can be used with this installation is 12 feet. This is based on the maximum allowable pressure drop of 0.5 pounds per square inch (psi) for fuel hoses at the flow rates typically used in aviation.
Fuel hoses are critical components in aircraft fuel systems. They are responsible for conveying fuel from the tanks to the engines, and they must be able to do so without leaking or becoming damaged. leaks orPoor performance can result in engine failure, which is why the design and construction of fuel hoses is of paramount importance.
Fuel hoses are typically made from synthetic rubber, which is resistant to fuel and oil. They are reinforced with fabric or metal braiding, and they are usually fitted with fittings on each end that attach to the fuel system components.
The pressure drop across a fuel hose is a function of its length, diameter, and the flow rate of the fuel. The maximum allowable pressure drop for aviation fuel hoses is 0.5 psi at the flow rates typically used in aviation. This means that the total length of fuel hose that can be used in an aircraft fuel system is 12 feet.
This 12-foot limit is based on the requirement that the pressure drop across the fuel hoses must not exceed 0.5 psi at the flow rates typically used in aviation. If the pressure drop across the fuel hoses exceeds 0.5 psi, the fuel flow to the engines will be reduced, and engine performance will suffer.
To ensure that the pressure drop across the fuel hoses does not exceed 0.5 psi, the total length of fuel hose used in an aircraft fuel system must not exceed 12 feet. This length limit ensures that the fuel hoses can convey the required amount of fuel to the engines without causing a significant drop in pressure.
Fuel hoses are critical components in aircraft fuel systems. They are responsible for conveying fuel from the tanks to the engines, and they must be able to do so without leaking or becoming damaged. The maximum length of fuel hose that can be used in an aircraft fuel system is 12 feet. This length limit ensures that the fuel hoses can convey the required amount of fuel to the engines without causing a significant drop in pressure.
A fresh viewpoint: Why Are Beds so Comfortable?
What is the minimum length of fuel hose that can be used with this installation?
The minimum length of fuel hose that can be used with this installation is 12 inches. This is based on the National Fire Protection Association (NFPA) code for fuel hose connection requirements. The NFPA code requires a minimum of 12 inches of fuel hose to be used when connecting a portable generator to a fuel supply. This is to ensure that there is sufficient hose to make a proper connection and to allow for any movement or vibration that may occur during operation.
What is the recommended width of the fuel hose?
The purpose of this document is to provide guidance on the recommended width of the fuel hose. Fuel hoses are used in a variety of applications, including automotive, marine, aviation, and industrial. The recommended width of the fuel hose depends on the application and the specific requirements of the engine.
For automotive applications, the recommended width of the fuel hose is 5/16 inch. This width is sufficient for most cars and trucks. For marine applications, the recommended width of the fuel hose is 3/8 inch. This width is sufficient for most boat engines. For aviation applications, the recommended width of the fuel hose is 1/2 inch. This width is sufficient for most aircraft engines.
The actual width of the fuel hose may be different than the recommended width, depending on the manufacturer. The width of the fuel hose should be checked before installation to ensure that it is the correct size for the application.
What is the recommended inside diameter for the fuel hose?
There is no definitive answer to this question as it depends on a number of factors, such as the type of fuel being used, the engine specifications, and the weather conditions. However, as a general rule of thumb, the inside diameter of the fuel hose should be around 8-10mm for light duty applications and 10-12mm for heavy duty applications.
What is the maximum length of the power wire for the fuel pump?
There is no definitive answer to this question as it depends on a number of factors, including the type and size of the fuel pump, the voltage of the system, the length of the run, and the wire gauge. In general, however, the maximum length of the power wire for the fuel pump should not exceed 50 feet.
Frequently Asked Questions
How do you fix a leaking fuel pump seal?
The Liquid Intelligence 229 Diesel Fuel Pump Seal Leak Fix formulation contains a unique combination of ester and phenol additives. When added to diesel fuel, the ester and phenol chemical combination swells and rejuvenates nitrile diesel fuel pump seals – completely eliminating leaks. If you do have a leaking fuel pump seal, we recommend using the Liquid Intelligence 229 Diesel Fuel Pump Seal Leak Fix.
How do fuel tank gaskets prevent leaks?
Gaskets are typically made of a rubber or plastic material that is sandwiched between two metal sheets. The metal sheets form the perimeter of the hole in the tank, and the rubber or plastic gasket prevents fluid from leaking out. By creating a tight seal between the metal and the rubber or plastic, it is difficult for fluid to leak from the tank.
How do you seal a plastic fuel tank?
1. Drill a hole large enough to allow the installation of a Fill Cap or Gasket 2. Open the Fill Cap or Gasket 3. Secure the cap withepoxy glue and let dry 4. Tighten fill cap or gasket securely
What kind of seals are on a diesel fuel pump?
On a diesel fuel pump, there are O rings that are made of FKM (also known as Viton) and those seals are not affected by the chemical changes in low sulphur diesel.
What to do if your diesel fuel pump seal is leaking?
Option 2. You could replace the seal outright with a new one, or have your diesel mechanic change it for you. Option 3. If Option 2 is not possible or desirable, you can add a -dye to your diesel fuel to hide any visible leaks. This will give you some temporary relief while you are waiting for the additive to work its magic.
Sources
- https://www.quora.com/What-is-the-big-deal-about-cutting-a-fuel-pump-access-panel-if-you-were-to-seal-it-properly-and-make-it-look-good-after
- https://diy-auto-repair.wonderhowto.com/how-to/lift-pickup-truck-bed-instead-dropping-tank-for-fuel-pump-access-396569/
- https://www.youtube.com/watch
- https://www.s10forum.com/threads/cut-hole-in-bed-to-replace-fuel-pump-fix-the-hole.864075/
- https://getjerry.com/questions/where-do-i-cut-in-my-truck-bed-to-reach-the-fuel-pump
- https://adslaser.co.uk/laser-cut-hole-diameter-per-material-type-thickness/
- https://www.youtube.com/watch
- https://www.ford-trucks.com/forums/562848-in-tank-fuel-pump-access-cut-a-hole-in-bed-floor.html
- https://www.ford-trucks.com/forums/1544036-cut-hole-in-box-to-access-fuel-pump.html
- https://www.gmtruckclub.com/threads/cutting-an-access-panel-to-replace-fuel-pump.38928/
- https://globalizethis.org/where-to-cut-hole-in-truck-bed-for-fuel-pump/
- https://www.ford-trucks.com/forums/255073-where-to-cut-holes-to-access-fuel-pumps.html
- https://club19golf.com/what-are-the-dimensions-of-the-holes-on-a-golf-course/
- https://www.s10forum.com/threads/should-i-cut-a-hole-in-the-bed-of-my-truck.218597/
Featured Images: pexels.com