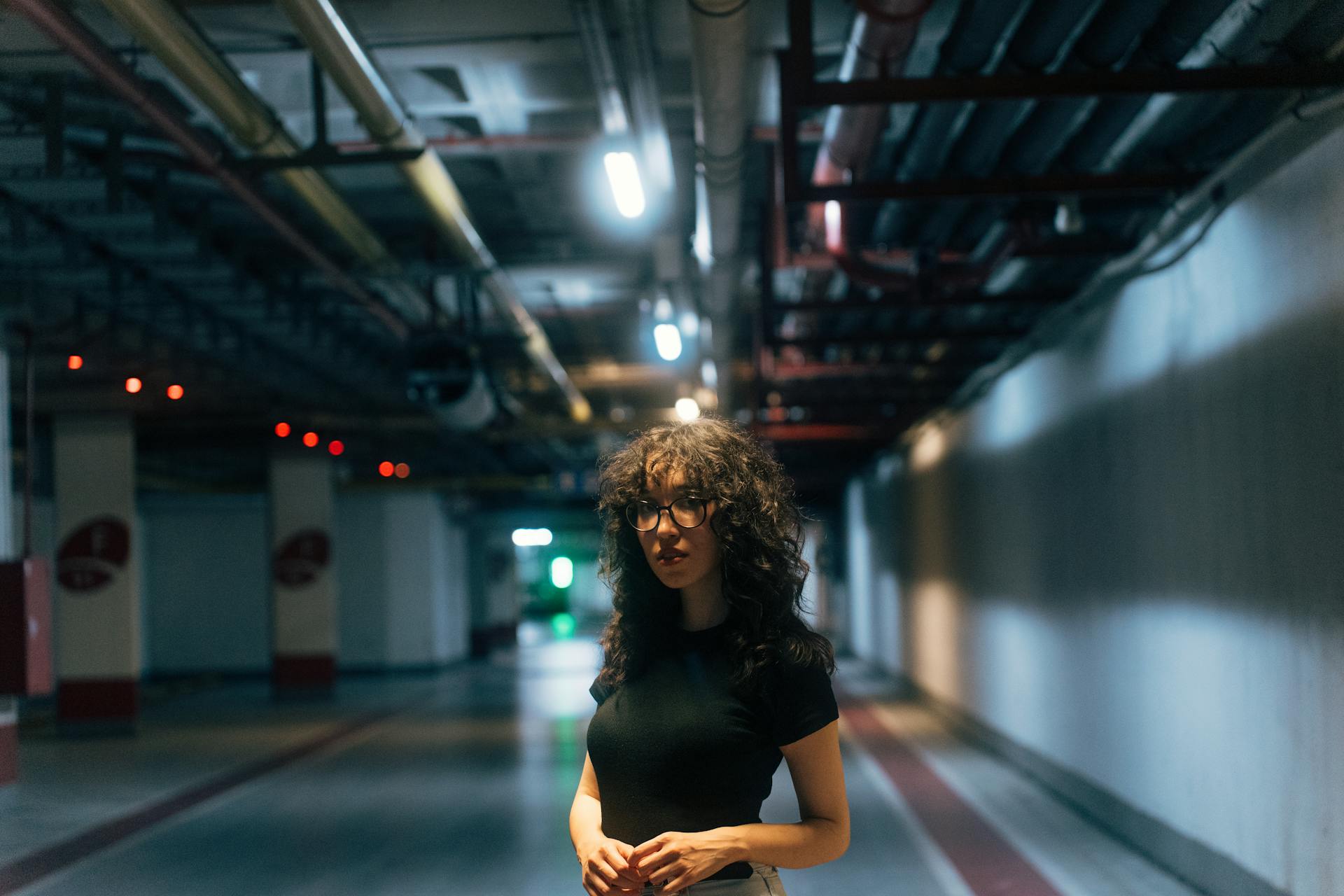
Installing insulation for underground water pipes is a crucial step in maintaining their integrity and preventing damage. This process involves wrapping a protective layer around the pipes to shield them from external factors.
The most common insulation materials used for underground water pipes are foam pipe insulation and fiberglass pipe wrap. These materials are effective in reducing heat loss and preventing ice from forming on the pipes.
Proper installation techniques are essential to ensure the insulation remains in place and functions as intended. This includes ensuring a snug fit around the pipes and securing the insulation with tape or wire.
Regular inspections and maintenance are also necessary to identify and address any damage or wear on the insulation.
Recommended read: Can You Put Insulation around Hot Water Pipes
Choosing the Right Insulation
Phenolic foam insulation is a great option for underground water pipes, offering a high R-value and low thermal conductivity. This type of insulation provides excellent protection against chilled water pipe condensation when paired with a quality vapor barrier.
Manufacturing phenolic foam insulation involves mixing a surface-acting compound with phenolic resin and solids, resulting in a network of microscopic bubbles that cures into foam insulation.
The insulation is shipped to the job site after gluing the vapor barrier jackets to the phenolic insulation sections. Contractors will seal the longitudinal seams of the insulation with mastic and the vapor barrier with self-sealing double-coated tape.
Some common materials used for insulation include foam pipe insulation, foam pipe elbows and tees, fiberglass tape insulation, foil tape, and cable zip ties.
Materials
When choosing insulation for your pipes, you'll want to make sure you have the right materials on hand.
Foam pipe insulation is a popular choice for long runs of water supply pipes, and it's available in eight-foot long tubes that can be split lengthwise for easy installation.
You'll also need some basic tools like a utility knife to cut the foam tube to length, and some tape to seal the seams.
If this caught your attention, see: How Long Do Copper Pipes Last with Hard Water
Foam pipe sleeves are another option, and they're available in 6-foot lengths that can be easily slipped over the pipe.
Most foam sleeves are made of foam or rubber insulation, and they come with self-sealing styles that make installation a breeze.
To install foam sleeve pipe insulation, you'll need to position the sleeves lengthwise along the pipe, pry open the slit, and slide the sleeve over the pipe.
You can also use foam pipe elbows and tees to make turns, or cut the sleeves at 45 degrees for a more complicated process.
Here are some common materials you'll need for insulation:
- Insulating pipe wrap
- Duct tape
- Foam pipe covers
- Frost-proof faucets (if desired)
Some other materials you might need include foam pipe elbows and tees, fiberglass tape insulation, and foil tape.
Additional reading: Tape for Water Pipes
Before You Begin
Before you start insulating your pipes, it's essential to consider the R-value of the insulation material. The R-value measures a material's resistance to heat flow, and a higher R-value means better insulating power.
Consider reading: Insulation Hot Water Pipes
The colder your climate, the higher the R-value you should look for when choosing pipe insulation. This is especially important if you live in an area with freezing temperatures.
Remove any dirt or grease from the pipes before insulating to ensure the insulation sticks properly. A quick cleaning with a dry cloth will make a big difference.
Make sure the pipes are completely dry before installing the insulation, as any moisture can cause it to come loose over time.
Installation and Protection
Chilled water pipe insulation can lessen the chance of frozen pipes in cold climates, particularly in uninsulated below-ground locations. This is especially important for areas with extreme temperatures.
You can protect your pipes with traditional pipe wrap insulation, which is available in various materials. These materials include flexible foam with rubber backing tape, foam-and-foil pipe insulation, and more.
To install pipe wrap insulation, start by duct-taping the end of the insulation strip to the pipe. Then, wrap the insulation around the pipe in spiral loops, overlapping each loop by at least 1/2 inch. This will ensure complete coverage of the pipe.
A unique perspective: Foam Insulation for Water Pipes
For longer runs of straight pipe, consider using foam pipe sleeves. These sleeves are available in 6-foot lengths and can be made of foam or rubber insulation. They're a simple and effective way to cover a lot of ground.
To install foam sleeve pipe insulation, position the sleeves lengthwise along the pipe and pry open the slit in the sleeve. Slide the sleeve over the pipe, and the slits will close up around it.
To secure the foam insulation, you can tie it with cable zip ties or wrap it every foot to 18 inches with foil tape.
Secure
Secure your pipe insulation with ease. You can use cable zip ties to tie the foam insulation in place.
Tying the insulation with cable zip ties is a great option. Alternatively, you can use foil tape to wrap it every foot to 18 inches.
Wrapping the insulation with foil tape is a simple process. Make sure to cover the entire length of the pipe to ensure maximum protection.
Securing the insulation is a crucial step in the installation process. By following these methods, you can ensure that your pipes are well-insulated and protected from the elements.
Consider reading: How to Install Heat Cable on Water Pipes
Using Foam Sleeves
Foam pipe sleeves are a simple and effective way to cover longer runs of straight pipe. They come in 6-foot lengths and are available in self-sealing styles, making them easy to install.
You can choose from foam or rubber insulation, and different diameters are available for different pipe sizes, including 1/2-, 3/4-, and 1-inch.
To install foam sleeve pipe insulation, position the sleeves lengthwise along the pipe and pry open the slit in the sleeve. Slide the sleeve over the pipe, and the slits will close up around the pipe.
Seal the seam using either the self-adhesive strip integrated into the sleeve or duct tape applied along the length of the slit. If necessary, continue with the next sleeve, butting it against the end of the previous sleeve.
At the end of runs, cut the foam tube to length using a utility knife. When the installation is completed, also tape the butt seams where two sleeves meet.
If the pipe is turning a corner, you can miter-cut the sleeves to fit around the corner, or use pipe-wrap to cover the fittings at corners, taping them to the foam sleeves.
Intriguing read: How to Cover Water Pipes outside
Bend Around Turns
You can bring foam pipe insulation around 90-degree bends, but it requires some extra effort. To do this, you'll need to cut one piece of insulation at 45 degrees using a square and utility knife.
Cutting at a 45-degree angle is essential to fit the two pieces of insulation together smoothly. This will ensure a snug fit around the bend.
You can also purchase separate foam elbows and tees that make the turns without the need to cut at angles. These are a convenient option if you're dealing with multiple bends.
To cut one piece of insulation at 45 degrees, use a square and utility knife. This will give you a clean and precise cut.
Here's a summary of the steps to bend foam pipe insulation around turns:
Thickness
Thickness is a crucial aspect of insulation installation. For insulation with a conductivity within the specified range, a minimum thickness or R-value is required, as shown in TABLE 120.3-A.
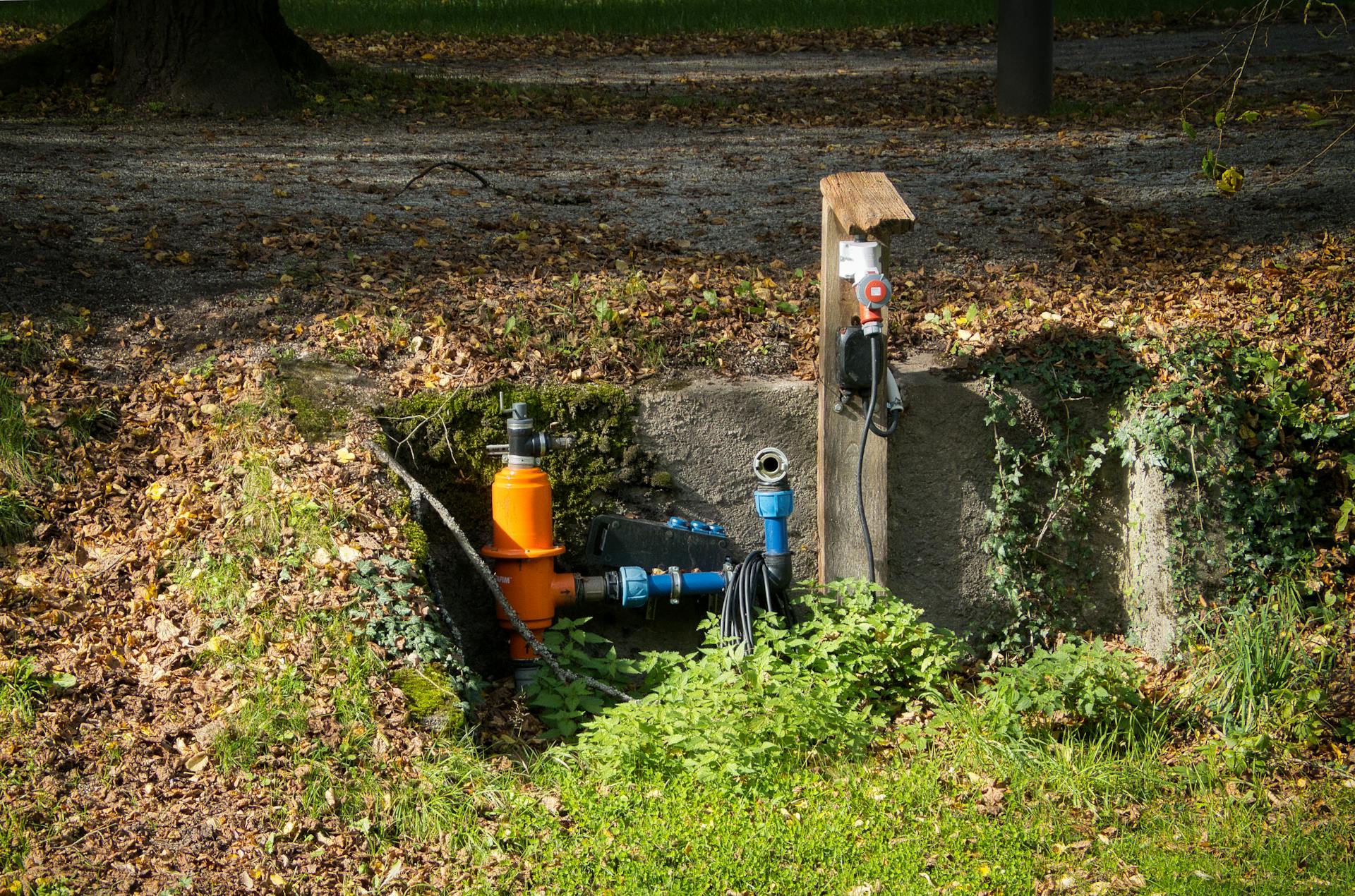
The table provides specific values for different fluid temperature ranges. If the insulation's conductivity falls outside this range, a minimum R-value or thickness must be met.
To calculate the minimum insulation thickness for materials with a conductivity outside the specified range, you can use the INSULATION THICKNESS EQUATION. This equation takes into account various factors, including the pipe's actual outside radius, insulation thickness, and conductivity of the alternate material.
The equation is complex, but it ensures that the insulation provides adequate protection against heat transfer. By using this equation, you can determine the minimum insulation thickness required for your specific application.
Here's a breakdown of the variables involved in the equation:
By understanding the requirements for insulation thickness, you can ensure that your installation meets the necessary standards and provides adequate protection against heat transfer.
Frequently Asked Questions
What is the best insulation to prevent pipes from freezing?
For outdoor water pipes, foam pipe sleeves made from flexible materials like polyethylene or rubber are a user-friendly and effective insulation option to prevent freezing. They provide a snug thermal barrier to maintain water temperature and reduce the risk of pipes freezing.
Sources
- https://www.forbes.com/home-improvement/plumbing/how-to-insulate-water-supply-pipes/
- https://www.thespruce.com/water-pipe-insulation-2718695
- https://polyguard.com/blog/chilled-water-pipe-insulation
- https://www.balkanplumbing.com/outdoor-pipe-insulation-water-lines/
- https://energycodeace.com/site/custom/public/reference-ace-2019/Documents/section1203requirementsforpipeinsulation.htm
Featured Images: pexels.com